Car: Toyota Supra 2JZGTE
Firmware: https://1drv.ms/u/s!Ao-FTTt3GMhrg4RGM1jTZZ0Ifn6c2g
OEM(Toyota) How it works
Actuators and VSVs:
They are not pulse width modulated except for the wastegate one. So the other 3 are either open or closed. The wastegate one is PWM controlled.
There are four VSV/actuator assemblies that control the sequential turbo operation:
[*]Intake Air Control Valve (IACV) --on/off
[*]Exhaust Gas Control Valve (EGCV)-- on/off
[*]Exhaust Gas Bypass Valve (EGBV)-- on/off
[*]Wastegate --PWM
VSVs switch manifold pressure (boost) to and away from actuators. The actuators open/shut valve butterfly flaps.
IACV
When this switches, boost generated by #2 turbo is allowed to join the intake stream
When it isn't switched, there is a small flap in the IACV assembly that allows any boost generated by #2 turbo as it prespools to join the intake stream, preventing turbo stall.
EGCV
This allows exhaust gas to flow through #2 turbo, causing it to spin up. When it's shut, there is no gas flow through the impeller of #2 turbo and therefore it doesn't spin.
EGBV
This allows some exhaust gas to bypass the EGCV and join the output of the first turbo. It serves two purposes - one, it prespools the second turbo by allowing some exhaust gas flow through it. Two, it controls the amount of exhaust gas going through the first turbo in much the same way as a wastegate - therefore controlling the maximum boost pressure generated by #1 turbo.
Wastegate
This bypasses exhaust gas from the first turbo, lowering the overall amount of exhaust gas going through *both* turbos and controlling the maximum boost pressure generated by both turbos in parallel.
Motec M130
[*]Low Side Ignition 7 -- IACV
[*]Low Side Ignition 8 -- EGCV
My understanding
My map has IACV and EGCV set to two Aux outputs , my understanding is the transition is regulated by the Manifold pressure 350kPa , constantly turbo one is working , when Manifold Absolute pressure hits 350kPa , turbo two comes online, I presume the manifold absolute pressure would read xxxkPa at a certain rpm @X% throttle , so when she reads 350kPa you know she is running 70% throttle / 3800rpm so has enough gas to flow turbo 2 , open VSV to allow exhaust gas through? Would gearing come into it, how did you know to choose 350kPa?
Was told this is incorrect the Duty cycle tables control the valves, OEM the transition from 1 to 2 Turbos happens at 3500 rpm
Graph look like parallel operation though, the Duty cycle tables to me run the Turbos in Parallel
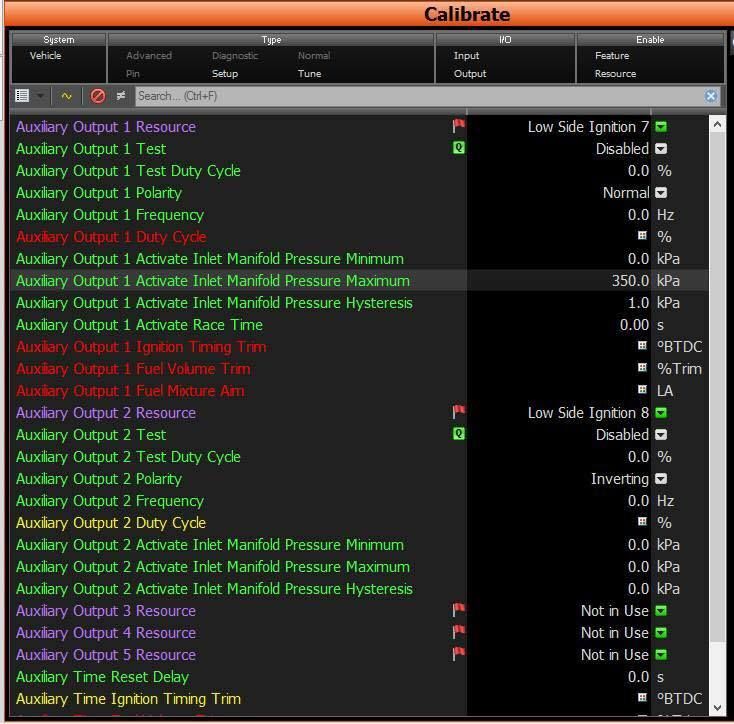
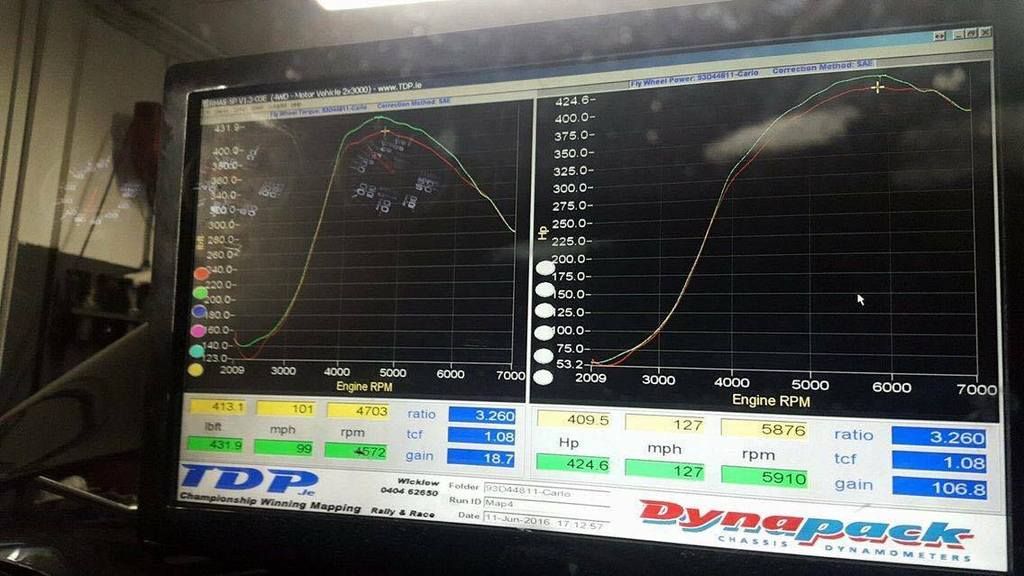
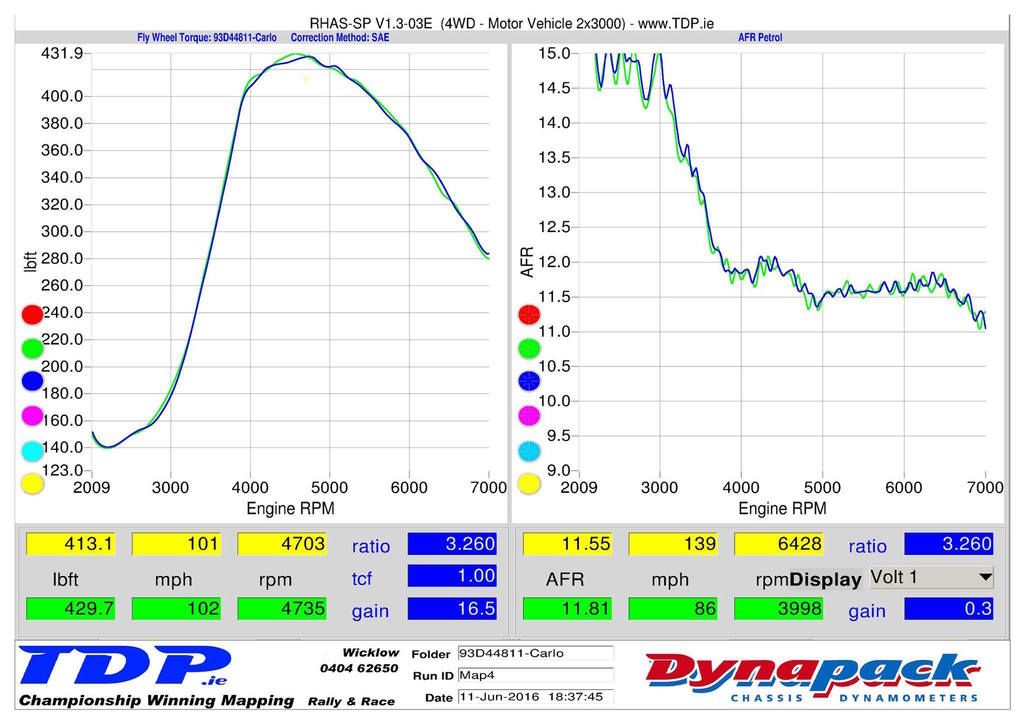
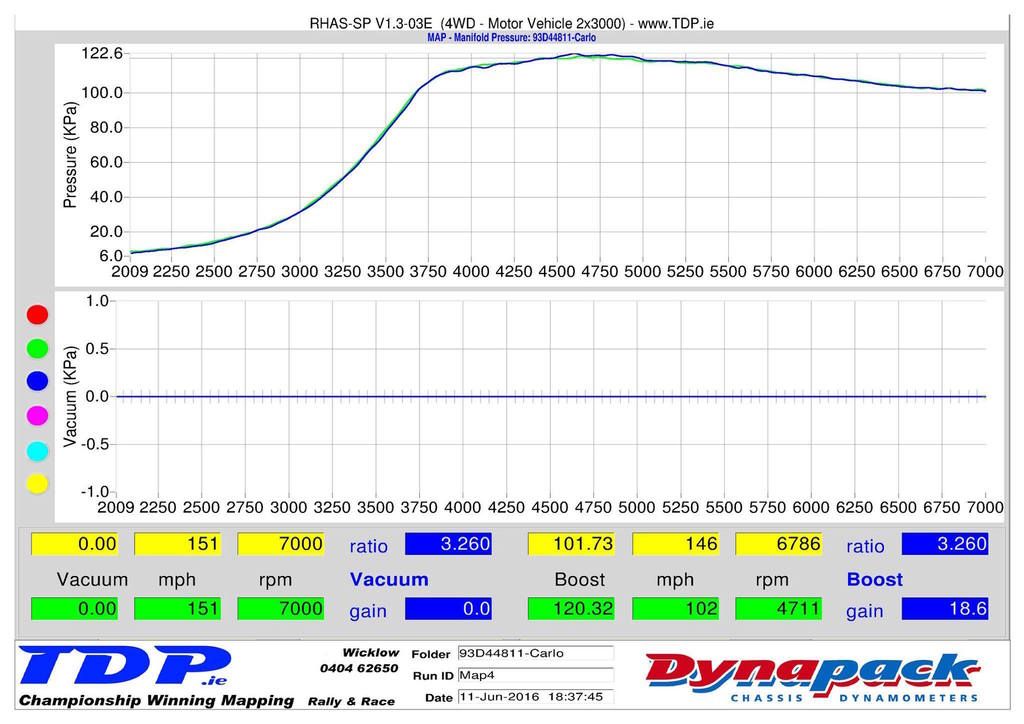
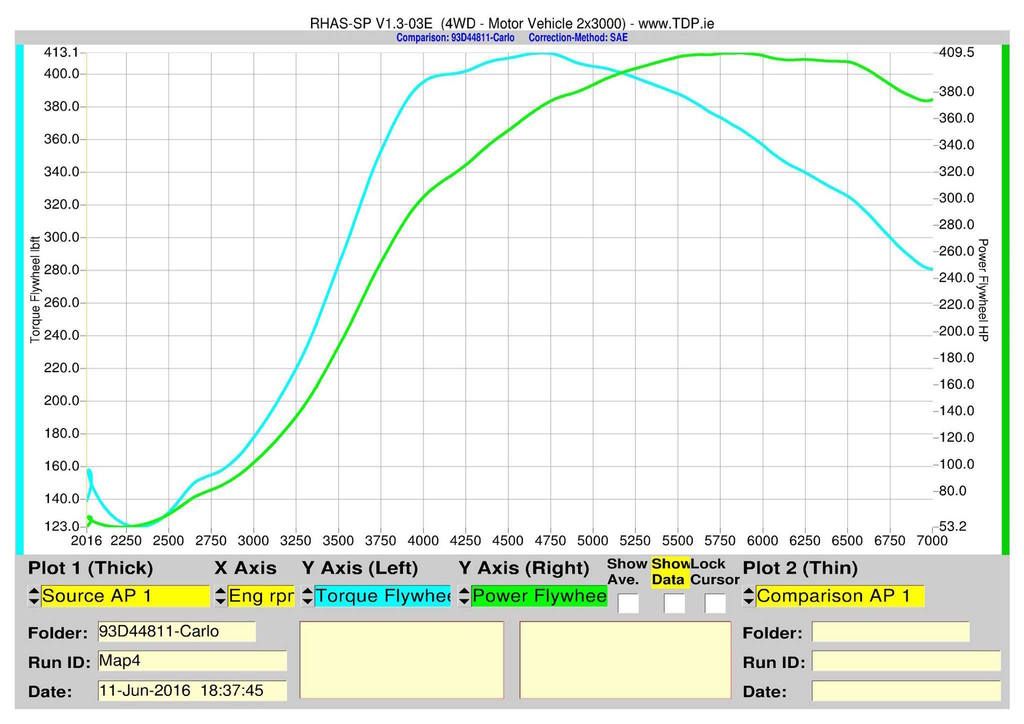
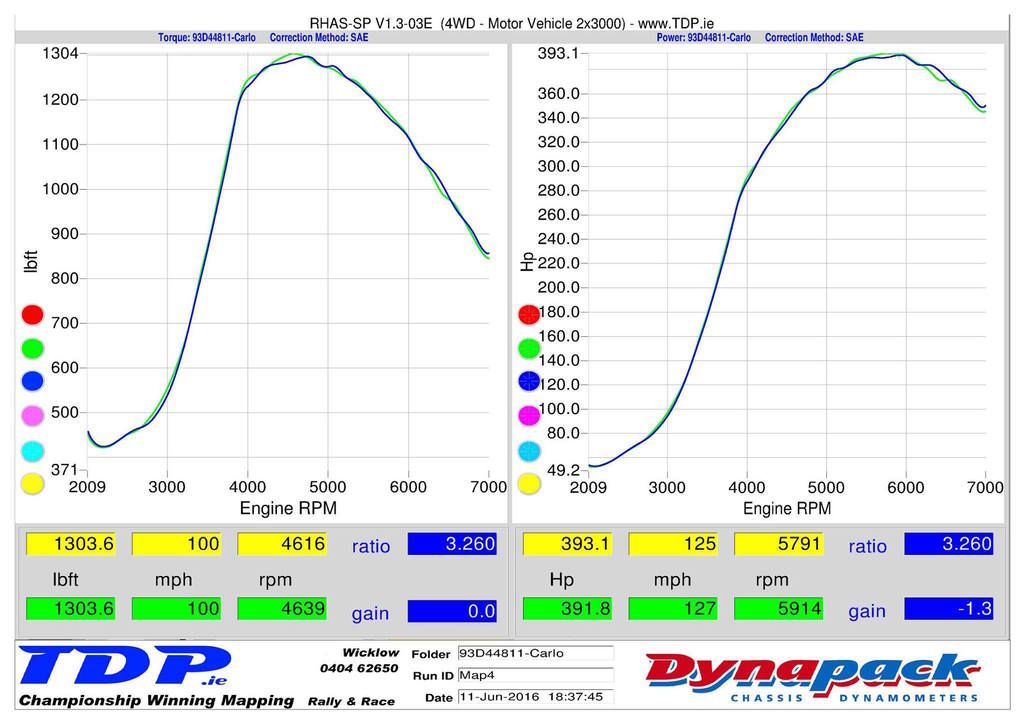
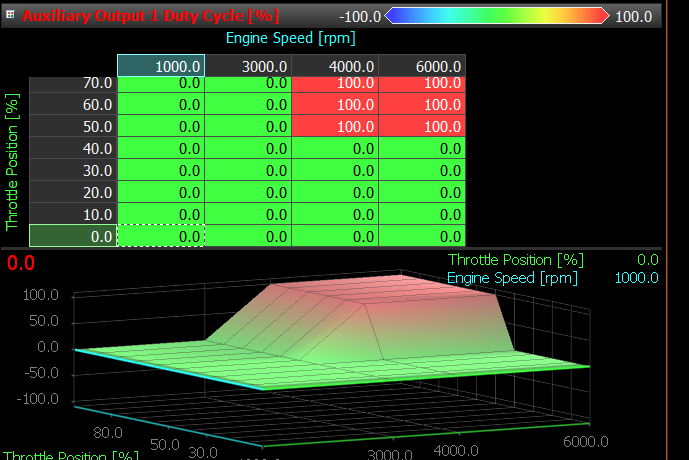
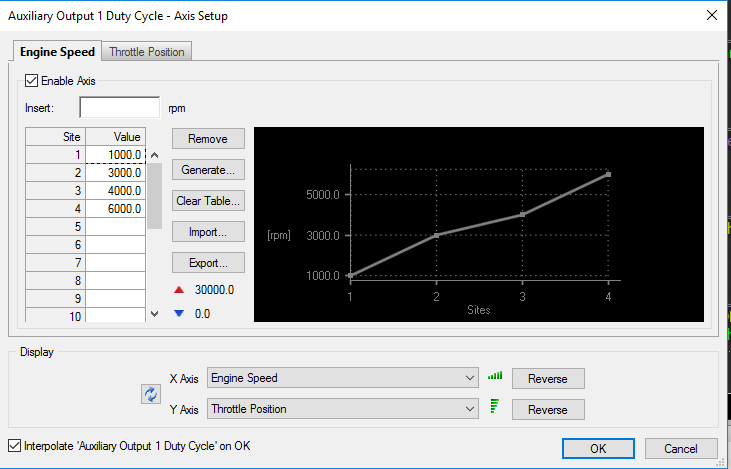
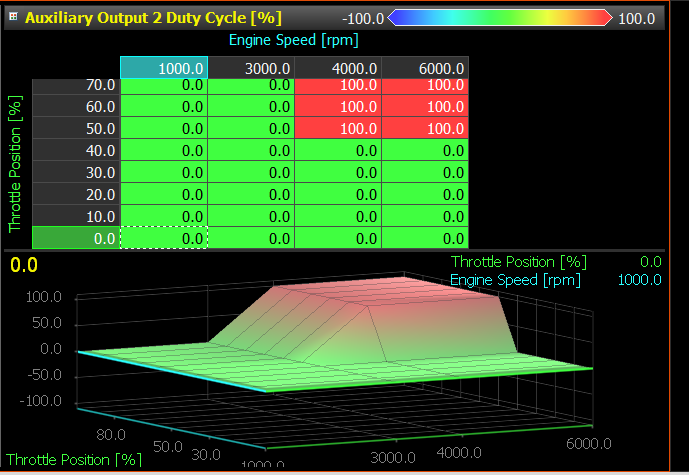
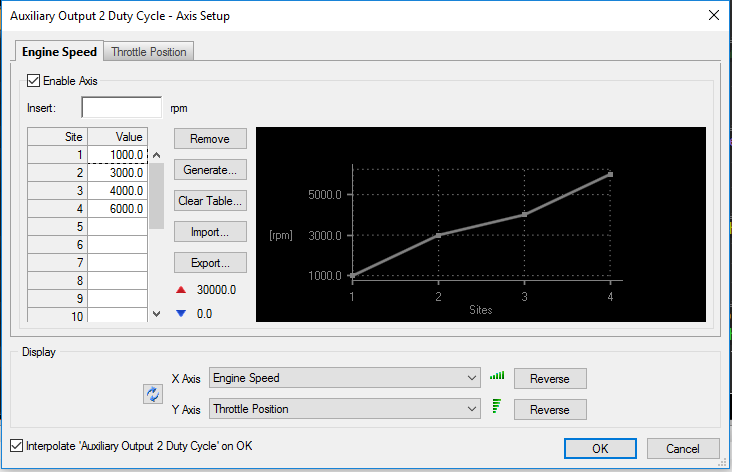